Qué es el cracking térmico y cuáles serán sus beneficios para Patagonia
Es una alternativa que se desarrolla en Plaza Huincul, Neuquén. Permite aprovechar los residuos plásticos que quedan en el ambiente
Los cientos de desechos de plásticos que son utilizados a diario y luego diseminados al aire libre sin que tengan un tratamiento definitivo para su eliminación pueden tener una vía sustentable. Se trata del cracking térmico, una alternativa que convierte el plástico en combustible.
Es el eje del proyecto que lleva adelante un grupo de investigación, surgido desde la facultad Regional del Neuquén de la Universidad Tecnológica Nacional, en Plaza Huincul.
El comienzo de esta propuesta data de 2015 y, desde entonces hubo avances significativos. El foco de la propuesta es darle valor agregado a la gran problemática que existe con los plásticos.
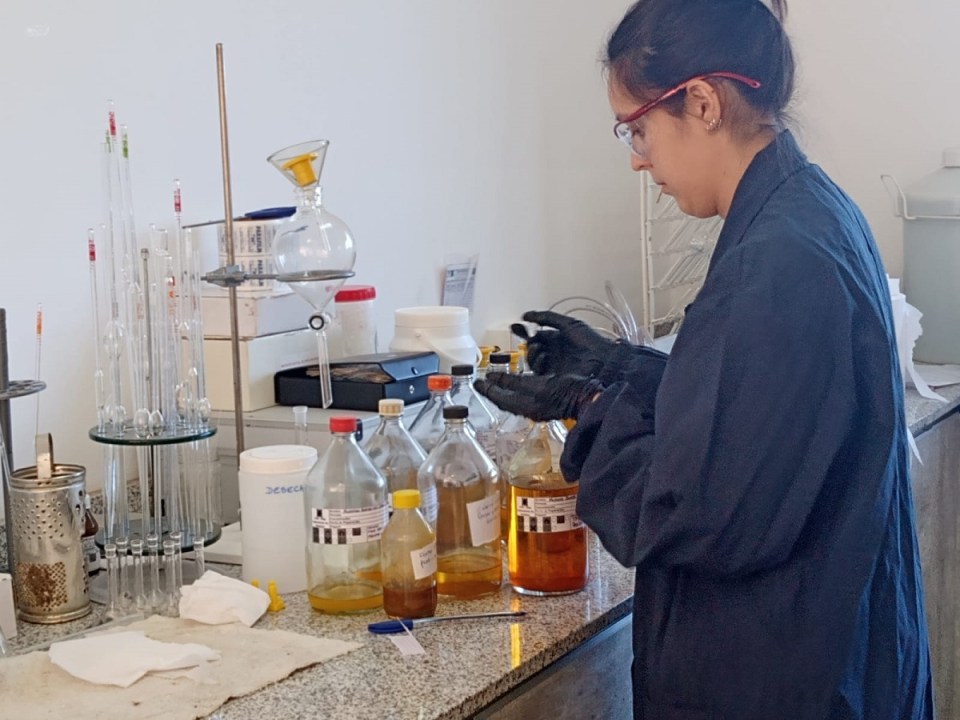
“Los océanos están llenos de plástico, hay islas de este material que tienen la superficie de hasta siete veces España. No se visibiliza mucho, pero la realidad es que están llenos”, describió la ingeniera Química, Gabriela Shell, una de las responsables de la iniciativa desde la UTN, en diálogo con RIO NEGRO.
La posibilidad de darle ese valor agregado al material plástico y transformarlo en gasoil es la razón principal del proyecto del cracking térmico, a través del reciclado químico se le puede dar la disposición final al plástico.
“Los plásticos son cadenas largas de carbono, enormemente largas y con el cracking las vamos cortando, en función de la temperatura y la presión. Se le da calor determinado y se la corta en la cantidad de carbonos que se necesite, de acuerdo al combustible que se quieras obtener”, explicó Shell.
“Hasta el carbono 4 se obtienen los gases, a partir del carbono 5 los líquidos y cuando se hacen cadenas más grandes de 30 a 40 se llega a los sólidos, hasta las ceras, por ejemplo”, detalló.
Al grupo de investigación le demandó un año –desde 2015 hasta agosto de 2016- llegar a la temperatura y presión justas para obtener el gasoil. Fue a prueba y error hasta que, a los 360 grados centígrados y hasta 365 grados y a una presión de 0,50 a 0, 70 kilos sobre centímetros cuadrados obtuvieron el combustible: gasoil.
Alcanzaron además una motonafta que “es como una nafta virgen” y los gases no condensables como etano, metano y propano que no es otra cosa que el gas de los hogares. En el fondo, lograron también una cera que puede ser utilizada como impermeabilizante de pisos o de calzado.
Shell describió que, de todos los combustibles que obtuvieron en el proceso de búsqueda, el gasoil resultó ser el fuerte porque el plástico ya viene refinado.
“El crudo que llega desde Vaca Muerta hasta una refinería hay que hacerle varios tratamientos previos, por ejemplo. Entre ellos, eliminar el azufre que es una de las variables más importantes a desterrar. Y el plástico ya no tiene niveles de azufre. Este gasoil no necesitaría ese proceso”, subrayó la experta.
Ese gasoil obtenido en la planta permitirá alimentar un generador; o destinado a las centrales termoeléctricas que usan fueloil y se podría utilizar como otro módulo dentro de las refinerías.
“Hay un nuevo concepto que son las biorefinerías y esta propuesta colaboraría haciendo un determinado combustible para derivar a otro módulo, lo pueden aditivar y obtener un producto más sofisticado. También podría estar en la cadena de una refinería”, sugirió la ingeniera.
La planta donde se realiza el proceso de cracking consta de las siguientes dimensiones: tres metros de alto por tres de ancho por tres de largo, es como si fuera un cubo. Consta de un reactor que es donde se hace el primer lote con los 200 kilogramos de plástico.
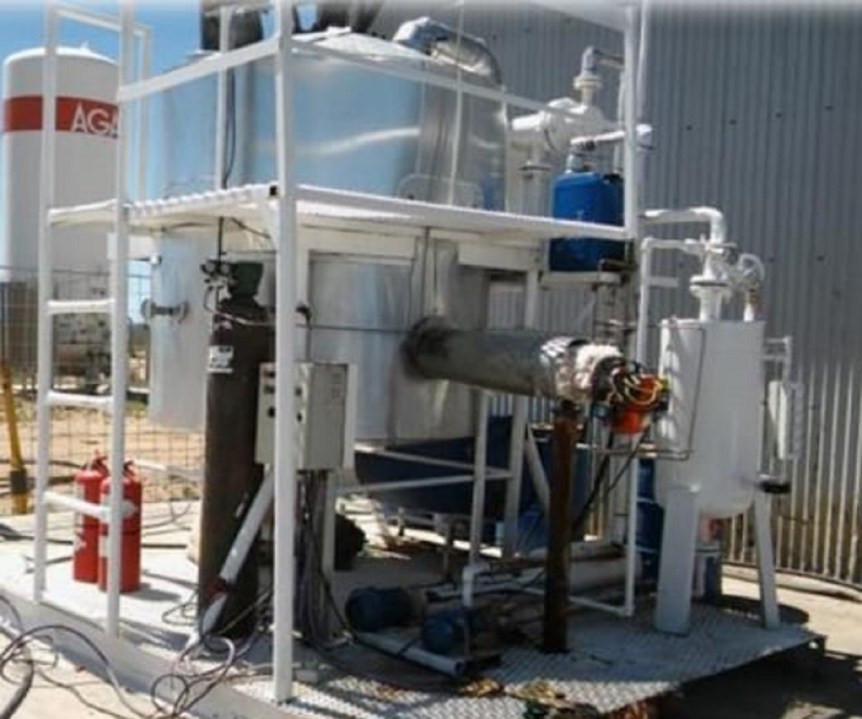
Se le aplica calor con un quemador; se derrite el plástico hasta llevarlo a más de los 360º y esos gases suben hacia un intercambiador, se condensan, vuelven a ser líquidos y quedan en un acumulador.
Luego, hay dos bombas que llevan la producción a un tanque de 200 litros y ahí se obtiene el producto crudo final.
Ese producto obtenido es trasladado hasta el laboratorio en la sede central de la UTN y se hace la destilación bajo las normas de rigor. Allí se obtiene el gasoil y la nafta virgen.
En las primeras experiencias pusieron a prueba el producto logrado cuando lo probaron en la propia planta que para el arranque requiere gasoil.
“Cuando obtuvimos el propio gasoil lo probamos en un generador y constatamos que tiene un octanaje interesante del orden de los 95”, refirió Shell.
En la actualidad, la planta de la iniciativa se encuentra en un sector del predio que INVAP tiene en el parque tecnológico de Cutral Co. Mientras que el laboratorio utilizado está en la sede central de la Regional del Neuquén de la UTN, en Huincul.
Este año quedó finalizado el espacio propio –dentro de la universidad UTN- y que la expectativa es que en tres meses esté en condiciones de ser utilizado. Aún falta el mobiliario como las mesadas, bachas, campanas extractoras, y otro mobiliario que será aportado por el municipio según el compromiso que asumió el intendente Gustavo Suárez.
Los próximos pasos
Este año se aguarda poner en marcha el convenio con la empresa YPF para que se puedan realizar ensayos con equipos que dispondrá la petrolera. “Veremos qué otros resultados nos arrojarán esos estudios para avanzar en la investigación”, relata la ingeniera que también lleva adelante un doctorado en el Conicet con este proyecto.
La primera etapa de la iniciativa fue la construcción de la planta. Desde ahora y a cinco años, el plan es poder rediseñarla para tenga la tecnología 4.0 y sea automatizada, a diferencia del método manual que tiene ahora.
Se apuntará a obtener el combustible ya en la planta y no llevarlo al laboratorio. Para ello se le tendrá que anexar –al dispositivo- una columna de destilación, que ya se modeló y se calculó la cantidad de platos necesarios y la altura.
En esta propuesta están los becarios de Ingeniería Química: Gastón Pincheira; Sheila Tagliapietra; Alén Verdugo; Micol Aguilera. Los becarios de la carrera de ingeniería Electrónica: Gonzalo Contreras y Maximiliano Antío mientras que el responsable del área electrónica es Raúl Espinoza. Mientras que a la doctorando Shell la acompañan como directora Mónica Gramajo y Alberto Camacho como codirector.
El último tramo del proceso será que tanto la planta como el laboratorio estén en un mismo espacio. La alternativa es que se pueda instalar en alguno de los parques químicos o tecnológicos de la comarca petrolera de manera definitiva. Mientras tanto, podría quedarse en un predio de los extalleres Plaza Huincul, en el barrio Central.
Las expectativas son que los ensayos en el laboratorio permitirán mejorar la planta. “Hubo dos donaciones de Techint en 2020 por 900 mil pesos y ahí logramos comprar dispositivos: una pantalla tácil, un triturador de 20 HP para tener mayor capacidad de trituración, un tanque de combustible más grande que cumple todas las medidas de seguridad, válvulas, mejoraríamos la perfomance, lo haríamos más automático el proceso”, acotó.
Ahora, recibieron la segunda donación de la misma empresa porque aplicaron a un programa es de 2 millones y medio de pesos para la compra de un destilador que irá en el laboratorio. Esto facilitará tener más automatizado el proceso.
Comentarios